124 workers died in work-related incidents in 2024/25

Latest annual figures show 124 workers were killed in work-related incidents in Great Britain from April 2024 to March 2025, representing a decrease of fourteen from the previous 12-month period. The Health and Safety Executive’s (HSE) annual fatality statistics indicate the number of deaths remain broadly in line with pre-pandemic levels, and compares to 223 twenty […]
HSE calls on employers to fulfil legal duties to mark Stress Awareness Week
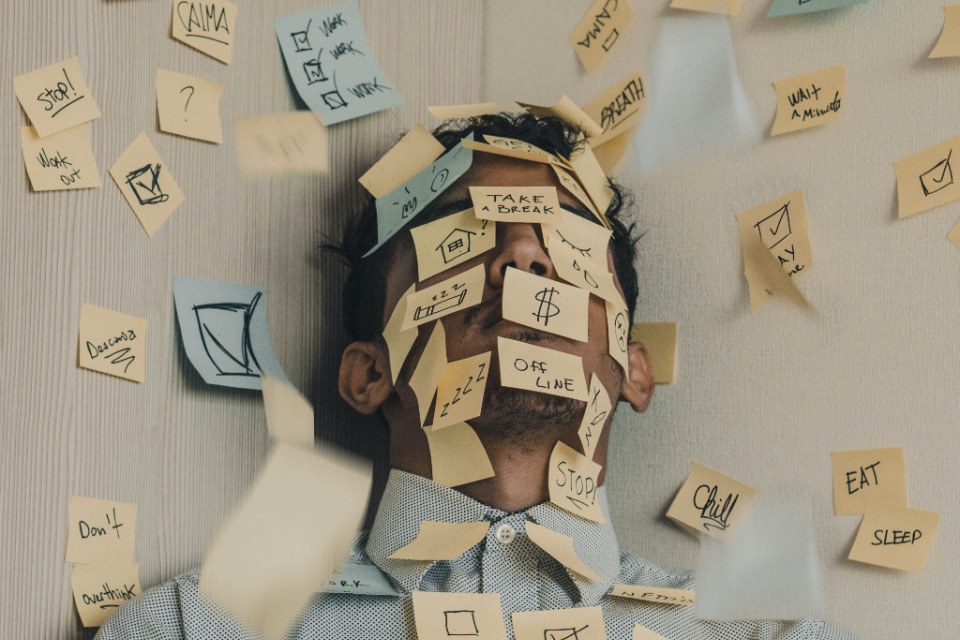
To mark Stress Awareness Week 2024 (Nov 4-8) the Health and Safety Executive (HSE) is calling on all employers to carry out their legal duty to prevent work-related stress and support good mental health at work. HSE figures show the average employee suffering from work-related stress, depression or anxiety took an average of 19.6 days […]
HSE data suggests continued high standards among building control professionals
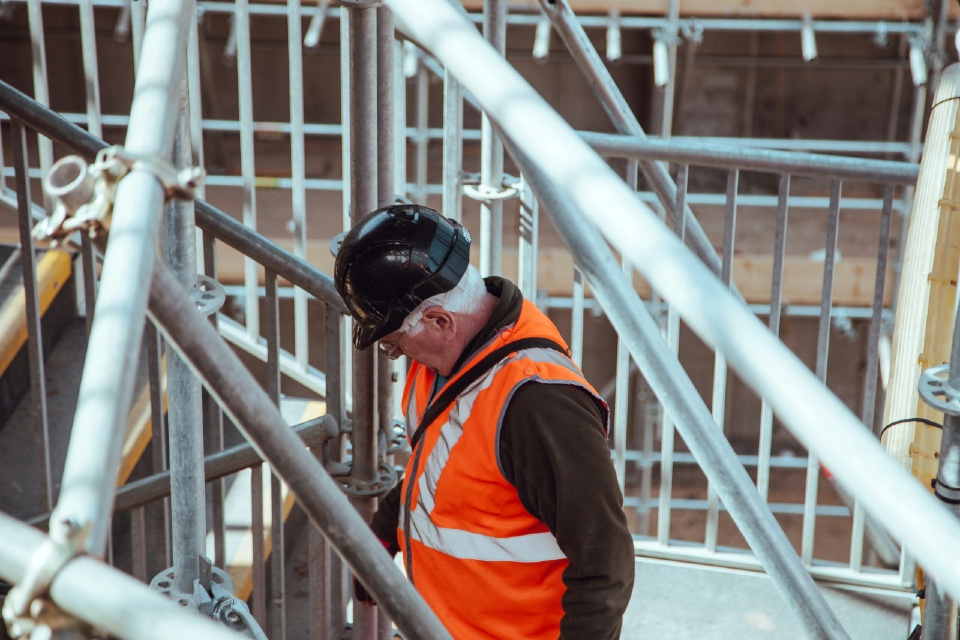
Building Control registration data indicates a growing number of professionals joining the registered ranks, reflecting the industry’s commitment to upholding high standards. The transition extension period ensured sector professionals had sufficient opportunity to align with the new requirements at a realistic pace without disrupting or compromising their ability to provide essential services. As of 30 […]
HSE inspection failure rates in spotlight

New research from BPD Zenith has found that nearly one fifth (17%) of businesses have received enforcement action in the past due to assets not meeting HSE compliance standards, with over 10% receiving an HSE fine. The research on 2,000 UK businesses surveyed organisations operating in the utility and renewable industries, including telecoms and broadband, […]
Construction industry rallies behind HSE mental health campaign
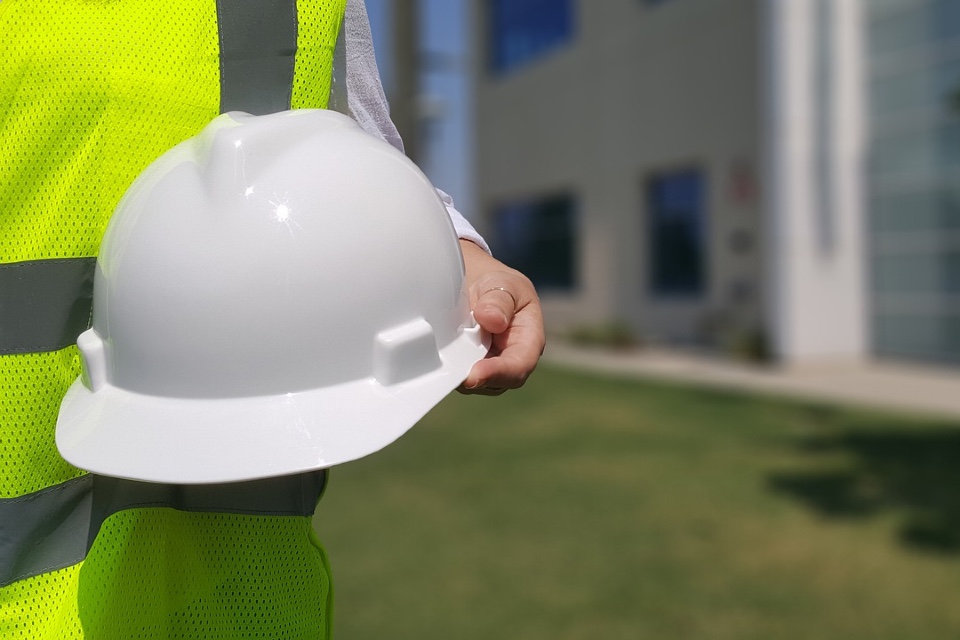
The construction industry has stepped-up its efforts to combat work-related stress and promote good mental health by joining the Health & Safety Executive’s (HSE) Working Minds campaign. March sees the Contract Flooring Association (CFA) and the Chartered Institute of Plumbing and Heating Engineering (CIPHE), Asbestos Removal Contractors Association (ARCA), the National Federation of Demolition Contractors […]
Work-related ill health hits 2m in 2022/23
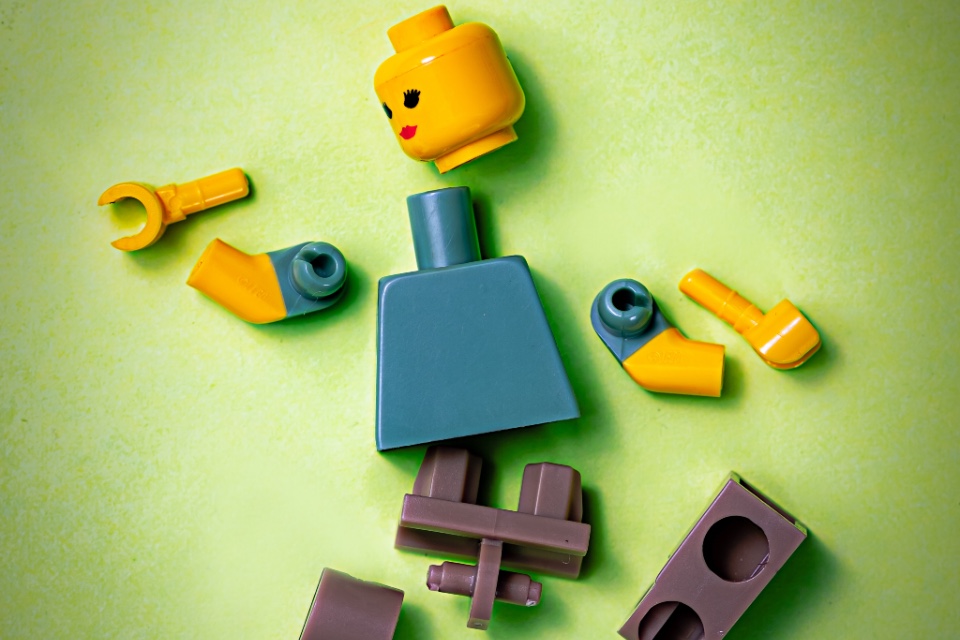
Nearly two million workers in Great Britain reported suffering from work-related ill health in 2022/23, according to the Health and Safety Executive’s (HSE) annual statistics on work-related ill health and workplace injuries. The statistics reveal that 1.8 million workers reported they were suffering from work-related ill health in 2022/23, with approximately half of the cases […]
HSE kicks off Working Minds campaign to improve truck driver safety
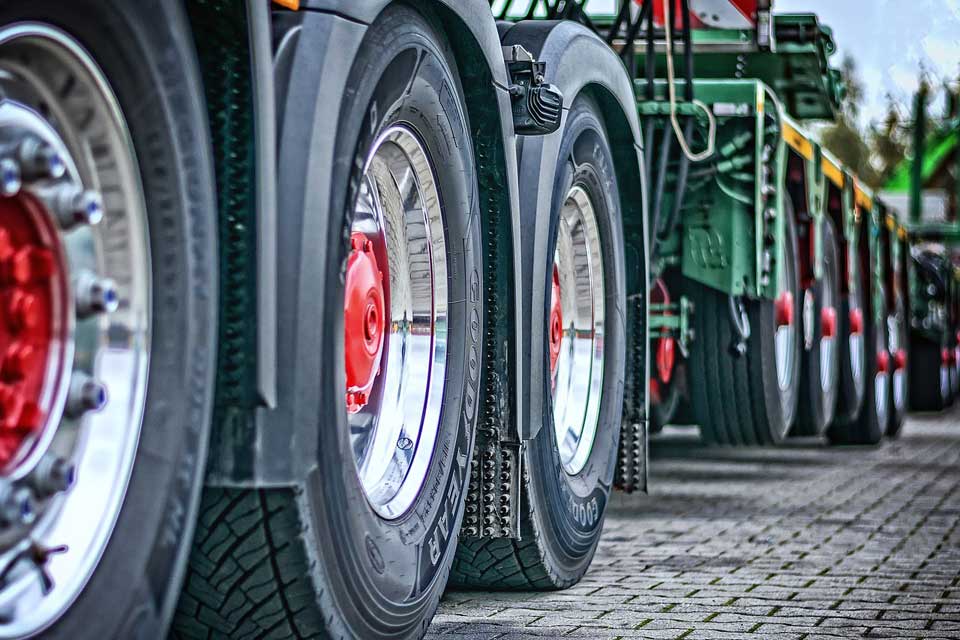
More needs to be done to protect Britain’s truckers from work-related stress according to the Health and Safety Executive (HSE), whose Working Minds campaign in partnership with the Road Haulage Agency is targeting drivers – and their bosses – to promote good mental health whilst at work. When safe to do so, drivers can text […]
Workplace complacency leading to a ‘safety plateau’
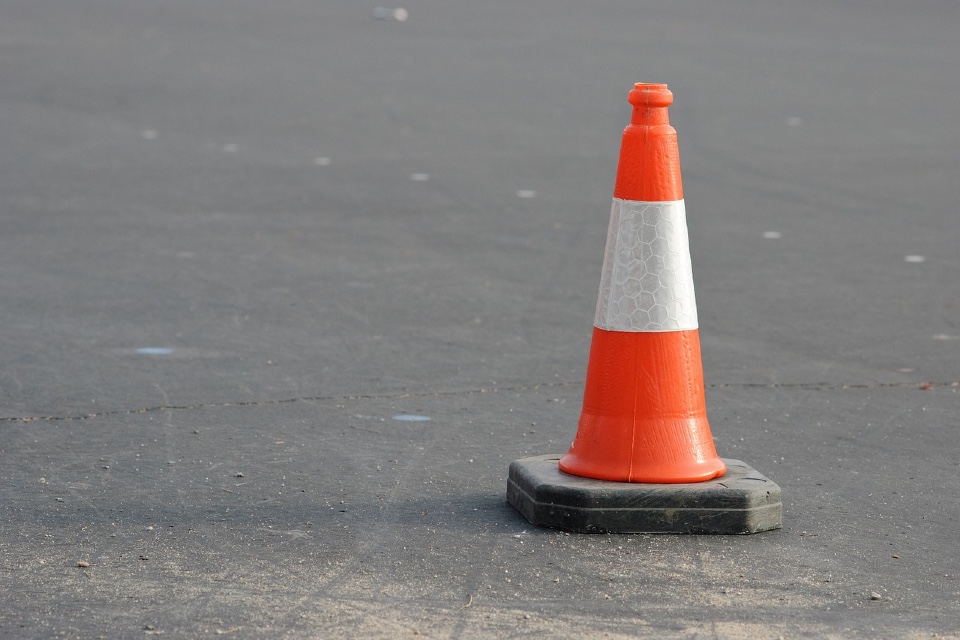
New statistics from the Health and Safety Executive (HSE) highlight a disheartening stagnation in the ongoing efforts to reduce work-related fatalities in Great Britain, according to a leading Health & Safety expert. According to the regulator’s latest report, a total of 135 workers tragically lost their lives as a result of work-related accidents between April 2022 and March 2023. Nick […]
HSE begins inspections of manufacturing for silica risks
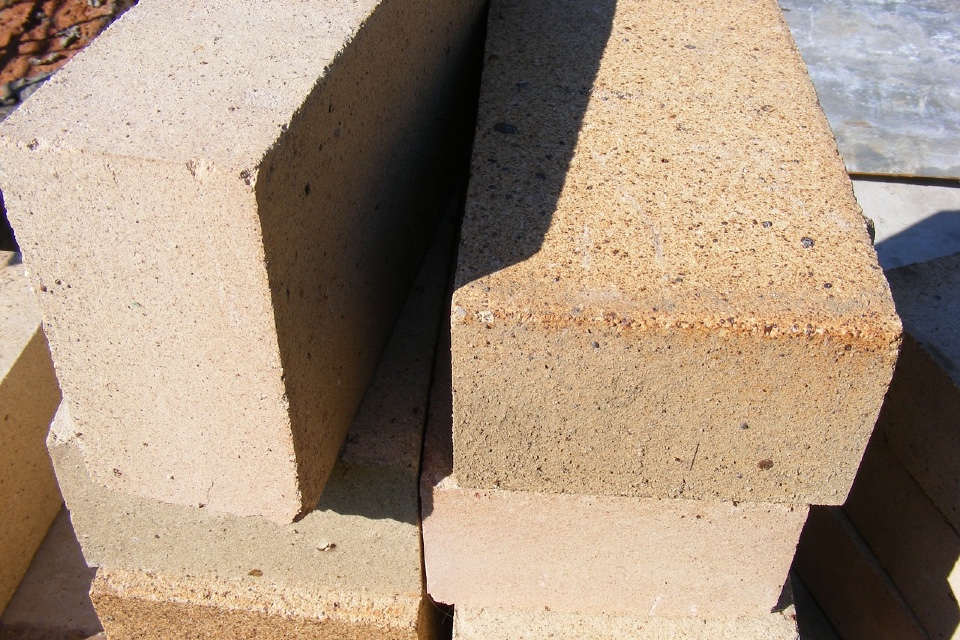
Health and Safety Executive (HSE) inspectors have begun a targeted inspection initiative focusing on manufacturing businesses where materials that contain silica are used, including brick and tile manufacturers and foundries. Exposure to airborne particles of respirable crystalline silica (RCS) can lead to life-changing respiratory conditions such as silicosis, chronic obstructive pulmonary disease and lung cancer. Silica is a […]
HSE shines spotlight on woodworking firms
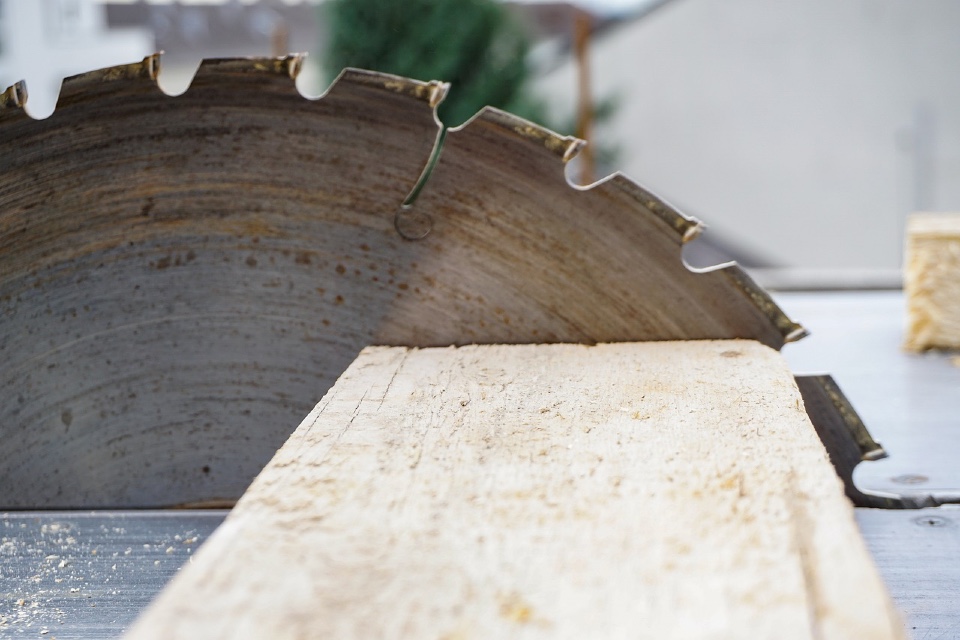
Many woodworking businesses are endangering workers’ lives by failing to implement the measures required to prevent or control exposure to wood dust, according to the Health and Safety Executive (HSE). Supported by HSE’s Dust Kills campaign, which provides free advice to businesses and workers on the control measures required to prevent exposure to dust, HSE […]