Work-related ill health hits 2m in 2022/23
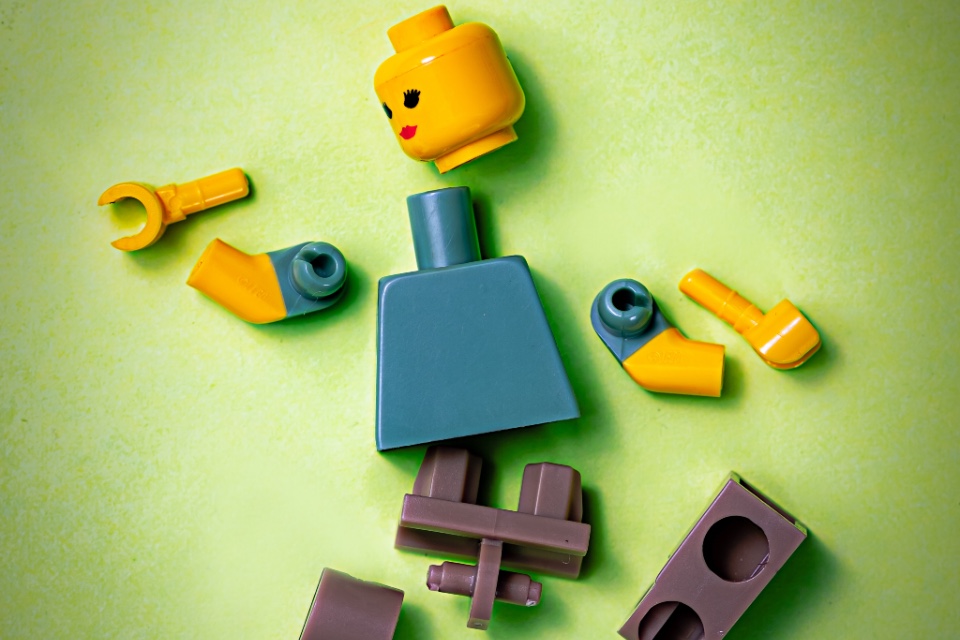
Nearly two million workers in Great Britain reported suffering from work-related ill health in 2022/23, according to the Health and Safety Executive’s (HSE) annual statistics on work-related ill health and workplace injuries. The statistics reveal that 1.8 million workers reported they were suffering from work-related ill health in 2022/23, with approximately half of the cases […]
Workplace complacency leading to a ‘safety plateau’
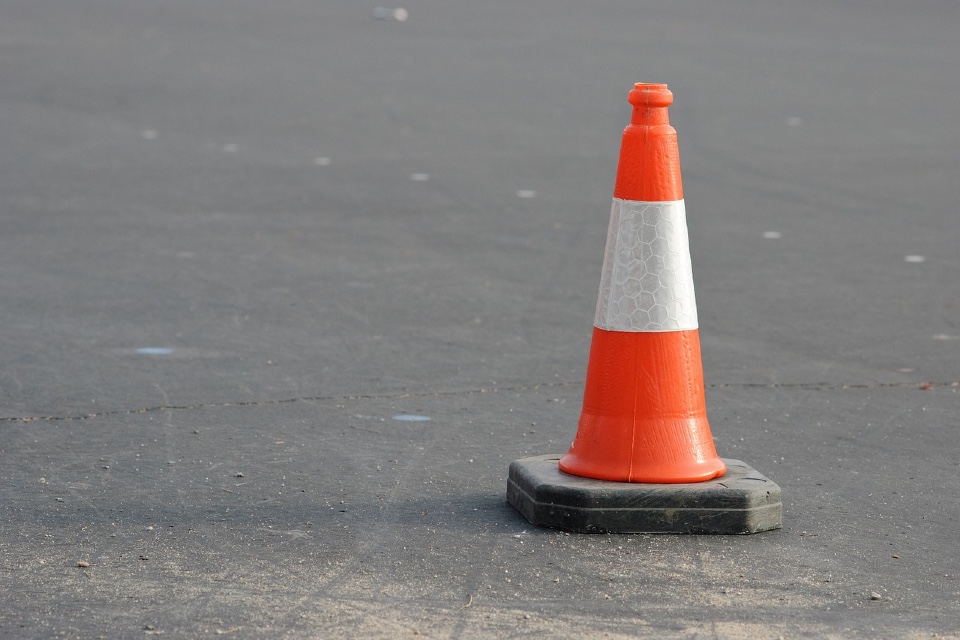
New statistics from the Health and Safety Executive (HSE) highlight a disheartening stagnation in the ongoing efforts to reduce work-related fatalities in Great Britain, according to a leading Health & Safety expert. According to the regulator’s latest report, a total of 135 workers tragically lost their lives as a result of work-related accidents between April 2022 and March 2023. Nick […]
Break free from the status quo! Transform your risk assessments with RiskPal
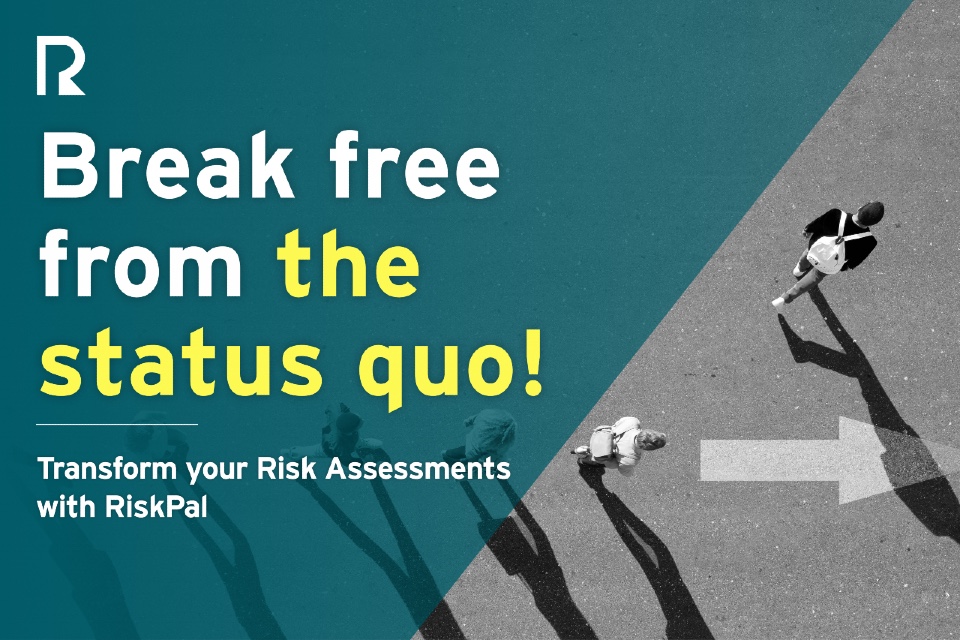
Time and again, Health and Safety professionals tell us the most common problems they face with risk assessment are: Receiving outdated, irrelevant or copied content Wasting time reformatting or updating unwieldy templates Chasing input and approval from management An inability to extract valuable health and safety data Missing oversight of all risk assessment documentation Sound […]
OPINION: Employee safety in the logistics industry starts with data collection and analysis

Logistics organisations are under unprecedented pressure to improve not only efficiency, but also employee safety. The COVID-19-inspired spike in demand has highlighted endemic performance problems and created new workplace challenges; how can companies recruit and retain staff in a highly competitive market when the transport and storage industry exhibits a higher rate of injury at all levels of […]
Scotland air pollution ‘concerning’

The British Safety Council says it is concerned by data analysed by Friends of the Earth Scotland, which showed that air quality breached legal limits during 2021 in Glasgow despite traffic levels continuing to be lower due to Covid restrictions. Peter McGettrick, Chairman of British Safety Council, said: “It’s concerning to see how air pollution […]
Why LEAD indicators allow you to elevate your health and safety organisation

By Steve Williams AMBCI, MIIRSM, Managing Director, BCarm 1 in 2 businesses say they don’t have safety performance metrics in place that allow them to measure and manage workplace safety every month*. Given the potential consequences of safety not performing, why wouldn’t you want to know how you are performing, and if you do, how […]
1.7 million workers suffering from a work-related illness, says HSE
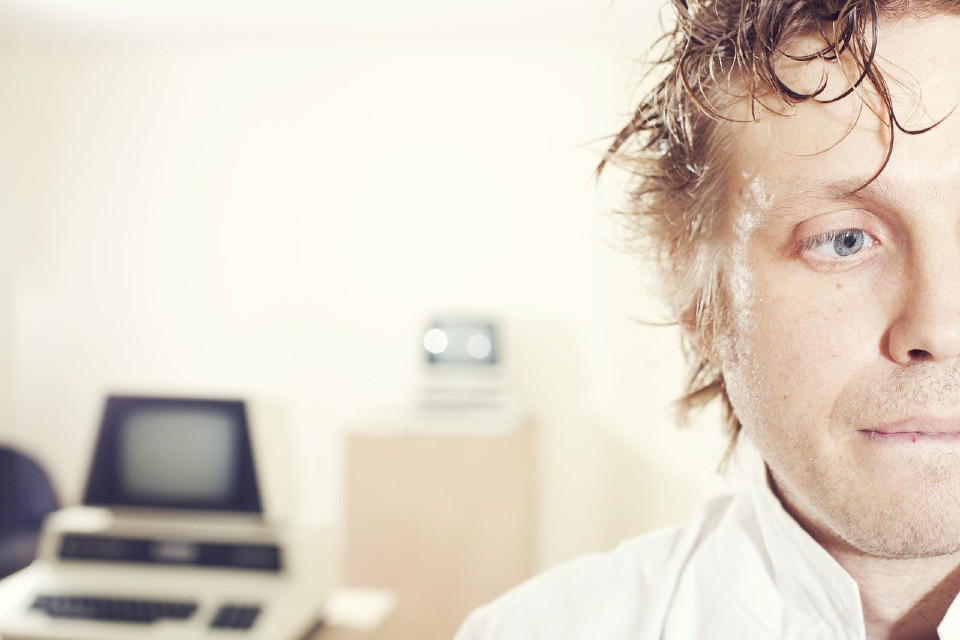
The Health and Safety Executive (HSE) has published statistics that cover work-related ill health, non-fatal workplace injuries and enforcement action taken by HSE, in the 2020/21 period. In total, 1.7 million workers are suffering from a work-related illness, around half of which were stress, depression or anxiety. In addition, two new estimates have been developed […]
WEBINAR REWIND: Learn how to transform your health and safety performance

Many businesses have performance data on sales, cash flow and stock holdings – but few have performance metrics on health and safety measures in the workplace. Find out how to unlock this knowledge in this unmissable webinar from BCarm. The webinar will give you practical take-aways on how to use metrics to transform your health […]